|
|
1.the
mine of clay:
The
extraction of the clay from the mine is made , in underground
galleries, by picking manually the rock. Then, the clay is
transported in baskets, and pile up. The piles of rough clay
are sold to the potters as raw material.
|
|
|
|
|
|
|
|
|
|
|
|
|
Shaping:
There are two ways to do it. The first consists in extending
the paste with the hands into long coils called " f' tila
" a coil is formed into a ring, the object is built up by
superposing a succession of rings that are then smoothed on
the wheel. This pottery-making technique " f' tila " is used
especially to built up large size items like the earthenware
jars and the large Amphoras.
With the use of the wheel it's possible to obtain regular
circular forms of differents sizes thanks to a skilful handling
of the clay paste and the speed of the wheel commanded generally
by the potter's foots.
|
|
|
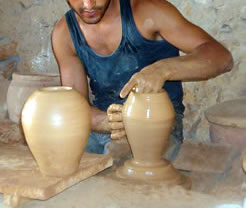 |
|
|
|
To avoid the breaks in Firing stage and to obtain solid
and consistent articles, our pottery is dried in the open
air for the small articles, or in cellars for the large ones
(earthenware jars,Amphoras), and that for one 21 days period.
Firing is made in traditional pottery furnaces under a temperature reaching 1200ー C. In reality Firing is
done in two times, the first time consisting in heating the
articles under a progressive fire going from 50ーC to 600ーC
during 48h, at this stage the flame is obtained from the combustion
of palm tree trunks. In the second time the temperature is
brought to 1200ーC thanks to the powerful flame of the palms,
and that during 10 hours.
|
|
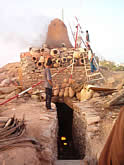 |
|
|